
PLASTICS

In today’s world of plastic materials there is an expanding array of characteristics for strength, abrasion and chemical resistance and heat tolerances. There are many variations of plastic materials and each one has their own set of properties. Why go plastic? It is cost effective, clean, lighter than metal, and versatile, depending on which plastic you choose.
With many years of experience in machining/fabricating with plastics, we have the knowledge to both improve on existing parts and offer advice for research and development. We can take your sketch and make it a reality. When specializing in plastic only; there will be no cross contamination risk FDA this material offers the food industry products that are chemical resistant, with great wear properties.

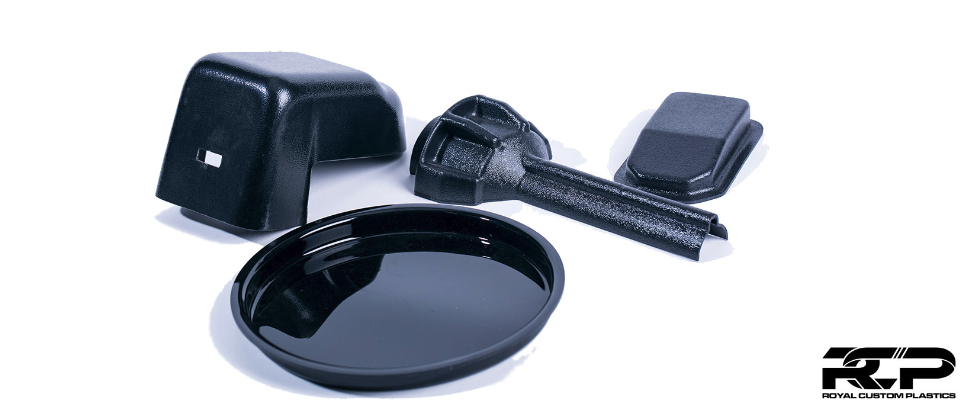
ABS
Acrylonitrile, Butadiene and Styrene are the three monomers that are combined to create ABS.
OVERVIEW
ABS is a Thermoplastic that offers heat and chemical resistance, high strength, and formability. It provides low temperature properties and electrical characteristics. ABS comes in a variety of grades such as, flame retardant, anti-static, chemical resistant, and abrasion resistant. As well as a wide range of colors, ABS can also come with textures that includes a Haircell/Smooth finish.
Royal Custom Plastics utilizes ABS for machined and fabrication jobs such as totes, guards, catch pans and much more!
HEAT & CHEMICAL RESISTANCE
ABS can be easily modified by adding additives and changing the ratio of the monomers. The modifications can then create grades that include high and medium impact, high heat resistance, and an electroplatable grade. The high heat grade can withstand temperatures up to 220° - 240° at a 264 PSI and 230° - 245° at 66 PSI.
MECHANICAL PROPERTIES
- Tough
- High Impact and Mechanical Strength
- Heat Resistant
- Formable
UL94 FLAME CLASSIFICATION
ABS is rated HB, horizontal burn; slow horizontal burn test are considered “self-extinguishing”. This is the lowest (least flame retardant) UL94 rating.
ACETAL
Acetal is a common name for a family of thermoplastics. There are two general types available: Acetal Homopolymer (POM-H), more commonly known as Delrin and Acetal Co-Polymer (POM-C).
OVERVIEW
Acetal is a Co-Polymer plastic that is known as POM-C. Although it comes in a variety of colors, the most common colors are black and its natural form, white. White Co-Polymer Acetal is FDA, USDA and 3-A Dairy Compliant.
Co-Polymer Acetal’s key properties include low moisture absorption, high mechanical strength and rigidity, good chemical resistance, and dimensional stability. It is also impressively effective when it comes to high heat and hot water performance.
Royal Custom Plastics utilizes Co-Polymer Acetal when machining bearings, bushings, rollers, belt guides, electrical components, wear strips, and much more!
HEAT & CHEMICAL RESISTANCE
- Resistant to a range of Chemicals
- Strength holds up to 180°
MECHANICAL PROPERTIES
- Good Wear and Abrasion Resistance
- Porosity Free
- Ease with Machinability
- Good Dimensional Stability
- Low Moisture Absorption
- High Strength and Stiffness
UL94 FLAME CLASSIFICATION
Acetal is rated HB, horizontal burn; slow horizontal burn test is considered “self-extinguishing”. This is the lowest (least flame retardant) UL94 rating.
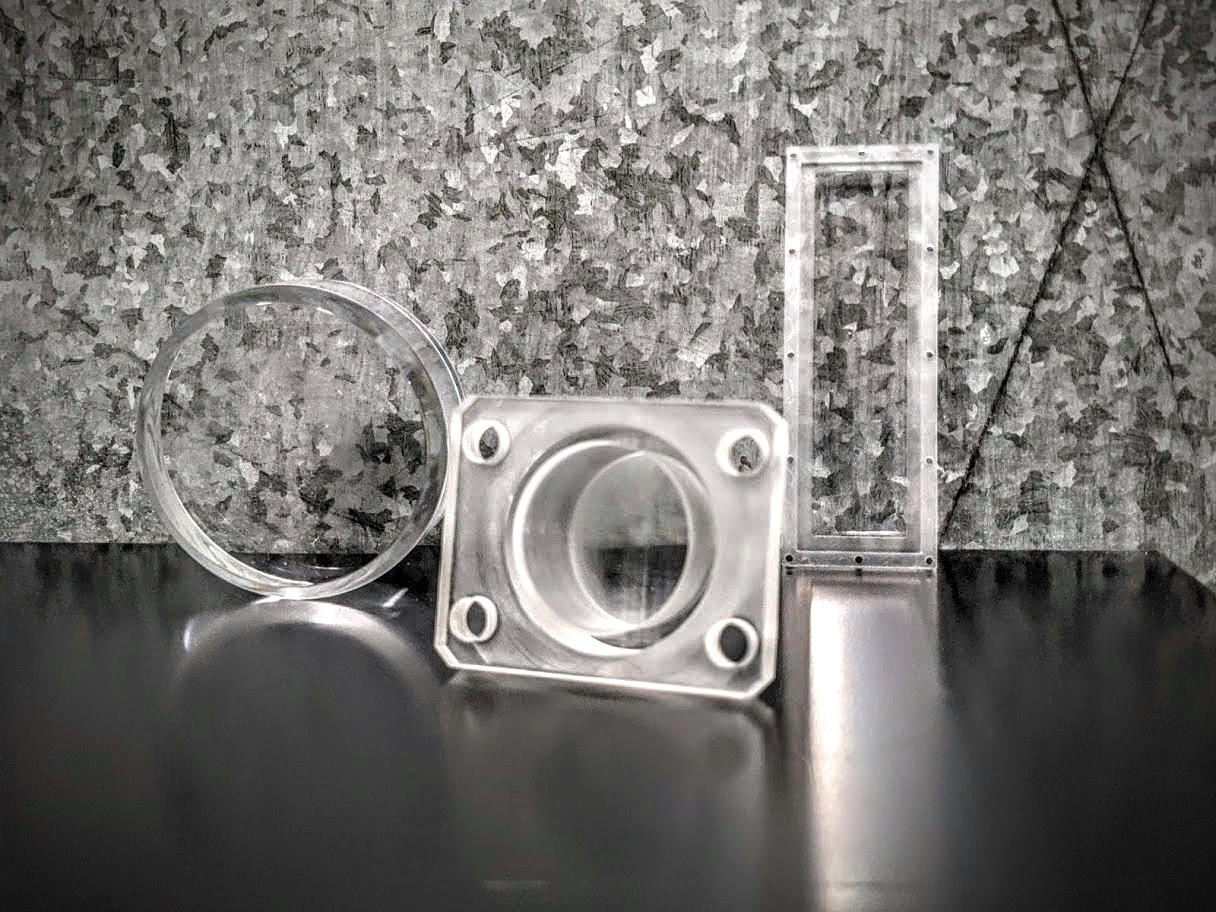
ACRYLIC
Acrylic, commonly known as Plexiglass, is one of the most familiar and multipurposed polymers used in construction materials.
OVERVIEW
Acrylic is dimensionally stable and shatter resistant. Unlike glass, it will not sliver when shattered, but will crack into large pieces. This thermoplastic is weather resistant and rigid. It is easily machined, heat formed, and cemented. Acrylic is more optically clear than glass with half the weight!
Acrylic comes in a variety of colors with variants of opaqueness ranging from clear to frosted and everything in between. Several textures are also available.
Royal Custom Plastics utilizes Acrylic for POP displays, windows, windshields, safety guards and covers.
HEAT & CHEMICAL RESISTANCE
Although Acrylic is chemical resistant, it should not come into contact with the following:
- Aromatic Solvents
- Chlorinated Hydrocarbons
- Ethyl and Methyl Alcohols
- Certain Organic Acids
- Lacquer Thinners, Ester, Ketone or Ethers
MECHANICAL PROPERTIES
- High Tensile Strength
- Good Electrical Properties
- Outstanding Weatherability
- High Optical Clarity
UL94 FLAME CLASSIFICATION
Acrylic is heat resistant up to 160° C and is rated HB, horizontal burn; slow horizontal burn test is considered “self-extinguishing”. This is the lowest (least flame retardant) UL94 rating.
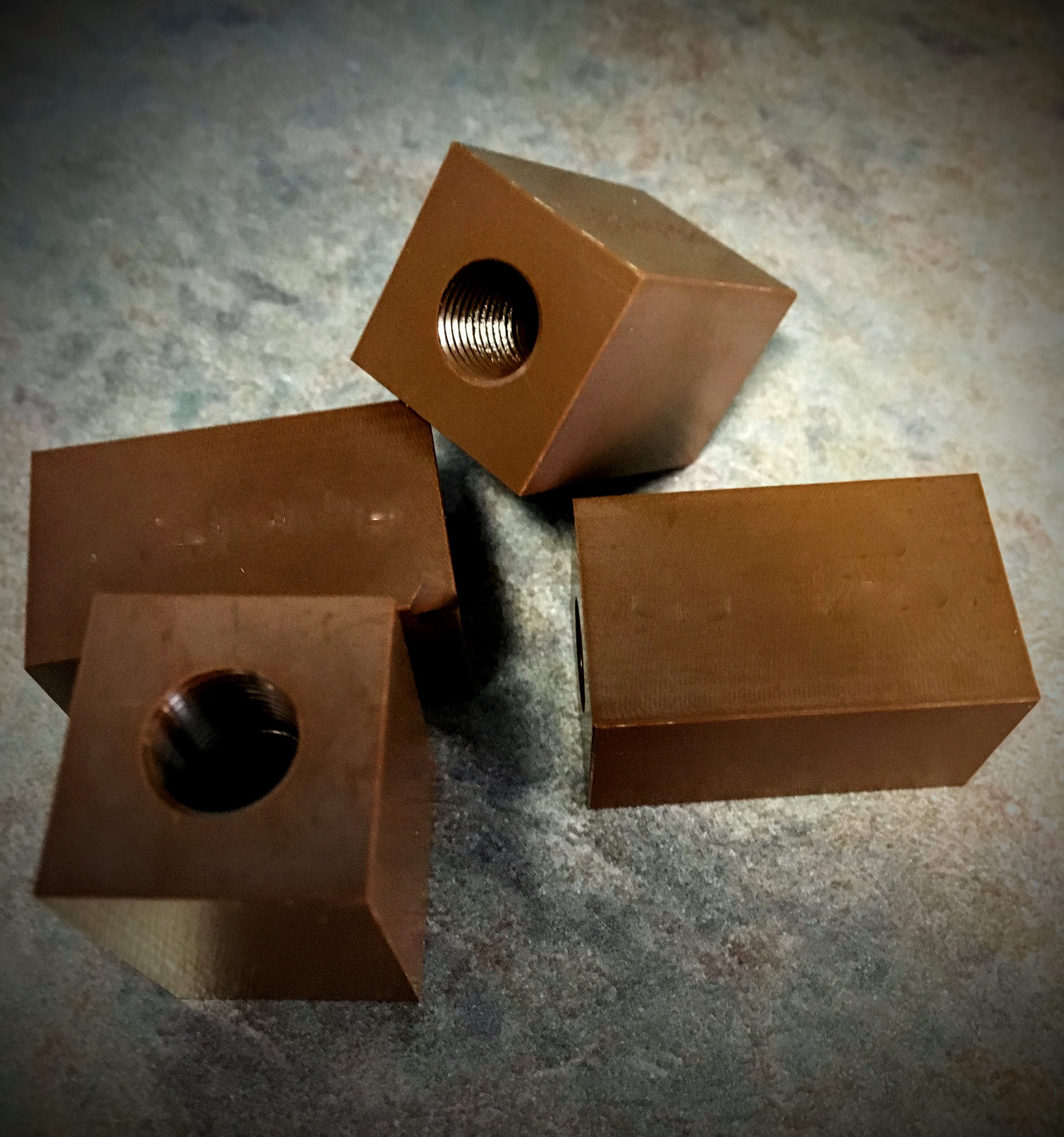
DELRIN
Acetal is a common name for a family of thermoplastics. There are two general types available: Acetal Co-Polymer (POM-C) and Acetal Homopolymer (POM-H), more commonly known as Delrin.
OVERVIEW
Delrin is a Homopolymer plastic that is known as POM-H.
Delrin has a high mechanical strength as well as, high fatigue endurance, creeper resistance and low moisture absorption. This material comes in Natural (white) and Black.
Naturally colored Delrin is FDA and USDA compliant.
One of its downfalls, is that it is not as chemically resistant as its Co-Polymer relation, Acetal. Additionally, during the process of producing Delrin, gasses fight their way to the surface causing pockets to form. This leads to a development of centerline porosity. With porosity comes weak spots. This can become problematic in a part that is designed for food processing and or medical applications since liquids can leak through the weak spots and create bacterial growth. Which is why Royal Custom Plastics only uses Delrin for applications such as gears, bearing, washers and rollers.
HEAT & CHEMICAL RESISTANCE
- Continuous Temperature of 185° F
- Resistant to a range of chemicals and many solvents
MECHANICAL PROPERTIES
- Excellent machinability
- High Fatigue Resistance
- Low Coefficient of Friction
- Good Surface Hardness
- Dimensional Stability
UL94 FLAME CLASSIFICATION
Delrin is rated HB, horizontal burn; slow horizontal burn test is considered “self-extinguishing”. This is the lowest (least flame retardant) UL94 rating.
ERTALYTE PET-P & ERTALYTE TX PET-P
Ertalyte PET-P is a poly-based thermoplastic that is semi-crystalline and unreinforced. It is known for its creep resistance, toughness, high dimensional stability, and low moisture absorption. Ertalyte PET-P comes in natural (White) and black color. Both colors are FDA compliant but only the natural color is USDA, 3A-Dairy and Canada AG compliant. Ertalyte TX PET-P is available in an FDA approved light gray color.
OVERVIEW
Ertalyte PET-P is abrasion and chemical resistant, but it lacks resistance to strong acids and bases. This material has a high impact strength and rigidity and is also stain resistant. Ertalyte is virtually unaffected by moisture which leads to excellent mechanical and electrical properties.
Ertalyte TX PET-P is an internally lubricated thermoplastic polymer. With this added uniformly dispersed lubricant, Ertalyte TX PET-P has better wear and low coefficient of friction than Ertalyte PET-P.
Royal Custom Plastics utilizes Ertalyte for many things including knife guides, paddles, wear strips, bushings, bearing blocks and so much more!
HEAT & CHEMICAL RESISTANCE
- Continuous Service Temperature of 210 ° F
- Resistant to a Wide Range of Chemicals
- Not Resistant to Acids and Bases
MECHANICAL PROPERTIES
- Low Coefficient of Friction
- Good Chemical Resistance
- Excellent Wear Resistance
- Low Water Absorption
- Superior Dimensional Stability
UL94 FLAME CLASSIFICATION
Ertalyte PET-P and Ertalyte TX PET-P are rated HB, horizontal burn; slow horizontal burn test is considered “self-extinguishing”. This is the lowest (least flame retardant) UL94 rating.
HDPE
High Density Polyethylene, also known as HDPE, is a light weight, non-toxic, and non-staining Polyethylene that is FDA and USDA certified. It has more strength and stiffness than its predecessor, LDPE.
OVERVIEW
HDPE has excellent impact resistance and low moisture absorption which makes it a perfect candidate for machined or fabricated cheese molds, drip pans and tank liners, to name a few! HDPE’s natural color is white, but It comes in a wide variety of colors and textures as well. Textured surfaces include Cutting Board, Marine Board, Woodgrain and more.
Royal Custom Plastics utilizes this material to fabricate and machine custom spacers, covers, trays, belt guards, water tanks, segments and so much more!
HEAT & CHEMICAL RESISTANCE
- Resistant to Mild Acids
- Resistant to Solvents
- Can withstand temperatures up to 248° F
MECHANICAL PROPERTIES
- High Rigidity
- High Tensile Strength
- Impact Resistant
- Light Weight
- Low Moisture Absorption
UL94 FLAME CLASSIFICATION
HDPE is rated HB, horizontal burn; slow horizontal burn test is considered “self-extinguishing”. This is the lowest (least flame retardant) UL94 rating.
LDPE
Low Density Polyethylene, also known as LDPE, was the first in the Polyethylene family. LDPE is FDA and USDA certified which makes it a great option for medical equipment such as, Prosthetic appliances and Orthopedic products. It is most commonly used for toys, plastic bags, packaging and bottles.
OVERVIEW
LDPE is highly flexible, corrosion resistant, and has great resilience. When in film form it offers great optical clarity. Although LDPE has good resistance to chemicals, it can be attacked by strong oxidizing acids. When LDPE is exposed to ultraviolet light and certain chemicals it becomes susceptible to stress cracking.
HEAT & CHEMICAL RESISTANCE
- Can withstand continuous operating temperature of 160° F
- Chemical Resistant
- Unresistant to Strong Oxidizing Acids
MECHANICAL PROPERTIES
- Low Moisture Permeability
- Corrosion Resistant
- Corrosion Resistant
- Flexibility
UL94 FLAME CLASSIFICATION
LDPE is rated HB, horizontal burn; slow horizontal burn test is considered “self-extinguishing”. This is the lowest (least flame retardant) UL94 rating.
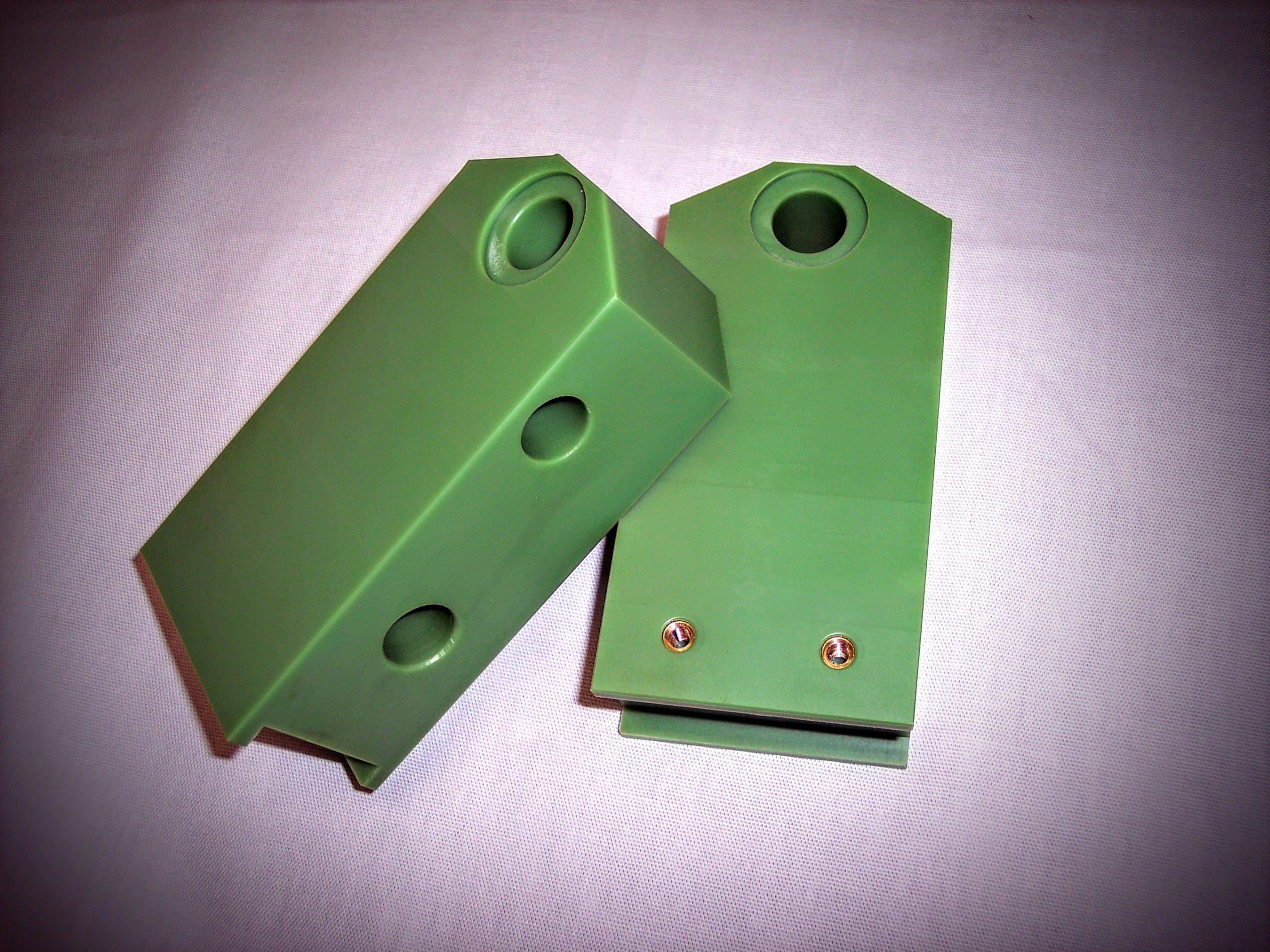
NYLON
Nylon is a widely used plastic for a variety of applications. Its exceptional strength, resistance to abrasion and wear and longevity are just a few reasons for it being the #1 choice for all industries. Natural Nylon is FDA and USDA compliant.
OVERVIEW
Nylons can also be combined with a large variety of additives to produce different variants with significantly different material properties. Here at Royal Custom Plastics, we utilize our vast knowledge of the different grades of nylon to best suite your applications. When it comes to the food/dairy industry, Natural Nylon could be used for paddles, conveyor side rails, wear strips and manifolds. For the paper/industrial industry, grades of nylon that include glass fiber, oil filled, and fiber reinforcement would be the ideal choice.
HEAT & CHEMICAL RESISTANCE
- Maximum Temperature of 210° F
- Melting Point of 420° F
- Good Resistance to most Chemicals
- Should not be used with Chemicals such as phenols, alkalis, iodine, and acids
MECHANICAL PROPERTIES
- High Compression Strength
- Impact and Wear Resistant
- Light Weight
- Lubricating Properties
- High Melting Temperatures
- High Impact Resistance
UL94 FLAME CLASSIFICATION
Although Nylon has a high melting temperature, it does not stand up well to an open flame. It is a flammable material and burns quickly when and if exposed to an open flame. Flame retardants can be added to the nylon to improve flammability. Because of the many grades of Nylon, please make sure to check on the UL94 rating for the grade of Nylon that you choose.
PEEK
PolyEtherEther-Keotone, more commonly known as PEEK, is a high-performance thermoplastic. Unfilled PEEK, aka general purpose, is FDA certified for food contact applications. It comes in natural (white) or black.
OVERVIEW
PEEK offers excellent chemical, water, radiation, and abrasion resistance. PEEK can run on a continuous temperature of 480° F in hot water or steam without permanent loss to physical properties. When looking for the strongest of the PEEK grades, turn to the general purpose, unfilled version.
Royal Custom Plastics utilizes PEEK in many applications including Industrial and Electronic.
HEAT & CHEMICAL RESISTANCE
- Outstanding Heat Resistance
- Great Chemical Resistance
- Exhibits very low Smoke and Gas Emission when Exposed to Flame
MECHANICAL PROPERTIES
- Low Moisture Absorption
- Good Wear and Abrasion Resistance
- Superior Strength to Weight Ratio
- Creep Resistant
- High Mechanical and Electrical Properties
UL94 FLAME CLASSIFICATION
Teflon is rated V-0, Vertical Burn. Burning stops within 10 seconds, no flaming drips are allowed.
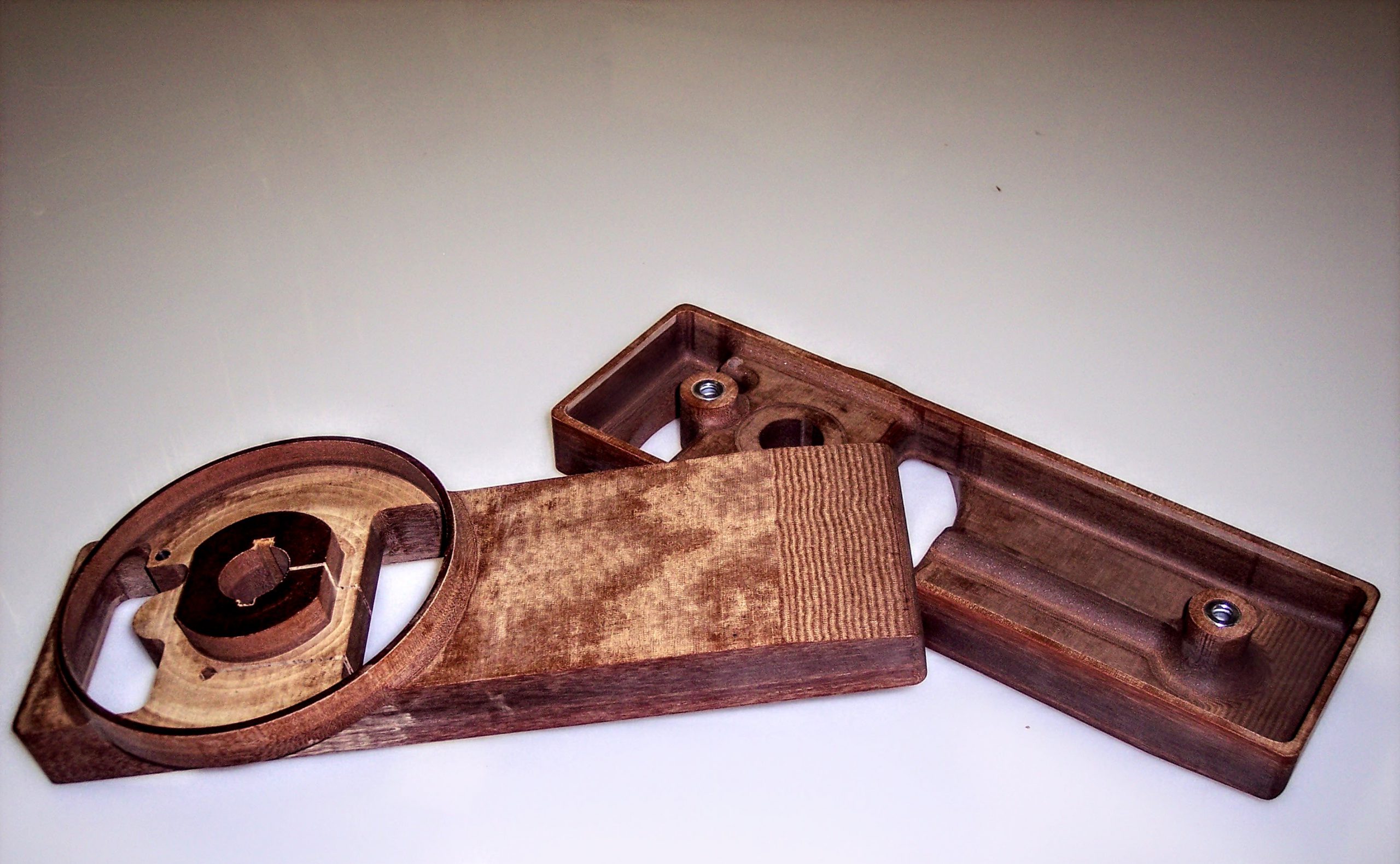
PHENOLIC
Under high heat and pressure, layers of cotton or linen canvas, glass cloth, or paper, are impregnated with thermoset resins to create Phenolic and its additional grades. These laminates are strong and durable while being lightweight and moisture resistant. Phenolics have high mechanical and isolating properties and cannot soften again. Phenolic laminates strength and stiffness leads to a high impact material.
Each grade of Phenolic has different strengths that offer an unlimited number of possibilities needed for the most difficult of applications. Below is the basic breakdown of the different grades of Phenolic and what they can offer.
GRADE C & CE
When the blend of medium weave cotton cloth fabric and Phenolic come together they create Phenolic C and Phenolic CE. This mixture provides a higher mechanical strength when compared to a paper grade. It also has a finer surface making it a superior machinable laminate. The toughness of this material is best suitable for applications requiring high impact strength. Grade CE is a great choice for electrical applications however, Grade C is not.
GRADE L & LE
A blend of Phenolic resin and fine weave cotton cloth fabric is what gives us Grades L & LE. Grade LE Phenolic is the same as grade L but with greater moisture retention which makes it the superior choice for electrical properties. The finely weaved cotton cloth base of both L and LE makes this Phenolic an even better machinable material than grades C & CE. When in need of more intricate details in your gears or pistons, Phenolic L & LE would be the best route.
GRADE X, XX & XXX
Paper mixed with Phenolic resin gives us Grades X, XX, and XXX. These are the most affordable grades in the Phenolic family. Each “X” represents a different level of dielectric strength and mechanical properties. Grade X has superb mechanical properties but is not suggested for applications where humidity is high and electrical properties are important. Grade XX is recommended for general electric insulations, while Grade XXX has superior electrical insulating strength and does well in high humidity, but its downfall is weaker mechanical properties.
GLASS PHENOLIC
G-7, G-10 and G-11 are made up of a mixture of either silicone or epoxy resin with glass cloth. G-7 is a glass-silicone laminate that has an excellent heat and arc resistance along with good electrical properties. G-7 is best used for electrical grade insulation, heating insulation and appliance insulation. G-10 and G-11 Phenolic has a mixture of epoxy resin and glass cloth. These laminates are known for their extremely high strengths and high dimensional stability over temperature, low water absorption, and superior electrical properties when both wet and dry. G-10 and G-11 are very hard to work with and usually require special tooling when machining. While G-10 is slightly stronger, G-11 can withstand higher temperatures and is a better insulator.
Royal Custom Plastics has utilized all grades of Phenolic for a wide range of applications including, insulators, cam followers, valve rings, gears, and housings to name a few.
MECHANICAL PROPERTIES
Phenolic CE:
- Good Mechanical Strength
- Low Cost
- Water and Chemical Resistant
- Low Moisture Absorption
- High Impact Strength
- Easy to Machine
Phenolic C:
- Water and Chemical Wear Resistance
- Low Cost
- Low Moisture Absorption
- Strong and Stiff
- Easy to Machine
Phenolic LE:
- Excellent Electrical Properties
- High Impact
- Compressive Strength
- Wear and Chemical Resistant
- Low Moisture Absorption
- Low Cost
- Good Mechanical Strength
Phenolic L:
- Good Chemical and Wear Resistance
- High Density
- Low Moisture Absorption
- Easy to Machine
- Low Cost
- High Impact Resistance
- Good Mechanical Strength
Phenolic X, XX & XXX:
- Great Wear and Impact Resistance
- Low Moisture Absorption
- Easy to Machine
- Good Mechanical Strength
- Strong and Stiff
- Least expensive of all the Phenolics
G7:
- Self-Extinguishing
- Excellent Heat and Arc Resistance
- Good Wet and Dry Electrical Properties
- High Density
- Strong
- Does not Soften under Reapplication of Heat
G10:
- Superior in Wet and Dry Electrical Properties
- Low Water Absorption
- Mechanical Strength
- Dimensional Stability
- Good Insulator
G11:
- Excellent Insulator
- Superior in Wet and Dry Electrical Properties
- Low Water Absorption
- Excellent at High Operating Temperatures
- Mechanical Strength
- High Density
- Good Dimensional Stability
UL94 FLAME CLASSIFICATION
G-7 & G-10 rating is V0, vertical burn; burning stops within 10 seconds, no flaming drips are allowed.
G-11 rating is HB, Horizontal burn; slow horizontal burn test is considered “self-extinguishing. This is the lowest flame-retardant rating.
POLYCARBONATE
Polycarbonate, commonly know as Lexan, is a tough engineering plastic. Its optical clarity and high impact strength make it a strong competitor for glass. Additionally, Polycarbonate has 250 times the impact strength of glass and 30 times the impact strength of acrylic.
OVERVIEW
Polycarbonate has great electrical and insulating abilities. It had 40% better thermal efficiency than glass and lower maintenance costs than both glass and acrylic. Polycarbonate is available in multiple grades to fit specific applications. Grades that are available help improve such things as chemical resistance, flame-retardant capability, FDA approved qualities, UV, and Abrasion resistance and many more. Polycarbonate also comes in a variety of tints, colors and textures including pebble, matte and prismatic.
Royal Custom Plastics utilizes Polycarbonate to fabricate and machine many different parts. Some of the parts we do are sight windows, guards, covers, guides, shields, enclosures and doors.
HEAT & CHEMICAL RESISTANCE
- Maximum Temperature is 250° F
- Melting Point is 300° F
- Resistant to Mineral and Organic Acids
- Resistant to Oxidizing and Reducing Agents
- Resistant to Greases, Waxes and Oils
- Not Resistant to Methyl Alcohol such as fuel, solvents, and anti-freeze
MECHANICAL PROPERTIES
- High Impact Strength
- Good Dimensional Stability
- Low Scratch Resistance
- Smooth Surface
UL94 FLAME CLASSIFICATION
Teflon is rated V-0, Vertical Burn. Burning stops within 10 seconds, no flaming drips are allowed.
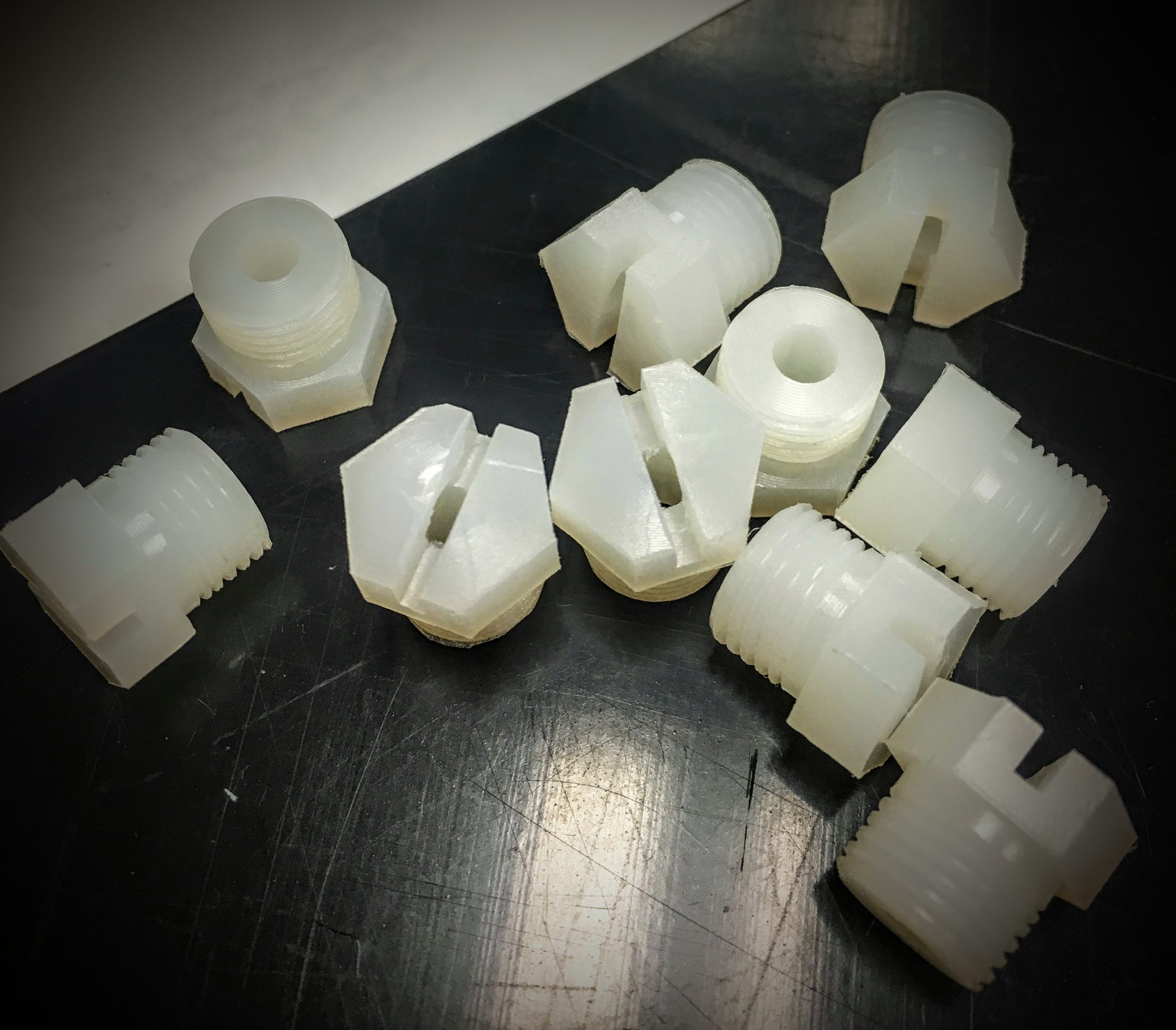
POLYPROPYLENE
Polypropylene is known for being the lightest plastic available. Its tensile strength and operating temperatures make it a superior choice when compared to HDPE and LDPE. Polypropylene has a smooth, hard surface which makes it ideal where there is a concern for bacterial build up. This material is approved for direct food contact.
OVERVIEW
Polypropylene comes in two different forms, Copolymer and Homopolymer.
Homopolymer Polypropylene (PPH) is the most common choice. It is stronger and more rigid than Copolymer. PPH has good chemical resistance and is ideal for both we and dry process applications. Because Natural colored Homopolymer Polypropylene is USDA, FDA, NSF and 3-A Dairy certified, it is an excellent choice for the dairy and agricultural industry. PPH comes in Natural (white) or black.
Royal Custom Plastics utilizes PPH for many things including, Tubs, Animal Feeders, Guards, Hoods, Tank Liners and Covers, Washers, Rollers and Gears.
Copolymer Polypropylene (PPC) has all the great qualities of Homopolymer Polypropylene with the addition of having a higher impact strength, greater flexibility, and lack of brittleness. PPC is very versatile while being inexpensive. It is FDA and 3-A Dairy Compliant.
HEAT & CHEMICAL RESISTANCE
- PPH – Operating temps range from 30° F - 180° F
- PPC – Operating temps range from -20° F - 180° F
- Resistant to: Acids, Alkalis, Organic Solvents, and Degreasing Agents
- Poor Resistance to Aromatic, Aliphatic, and Chlorinated Solvents
MECHANICAL PROPERTIES
- High Performance in Thermoforming
- High Performance in Corrosive Environments
- Good Weldability
- No Moisture Absorption
- Superior Tensile Strength
UL94 FLAME CLASSIFICATION
Polypropylene is rated HB, horizontal burn; slow horizontal burn test is considered “self-extinguishing”. This is the lowest (least flame retardant) UL94 rating.
PTFE / TEFLON
PTFE, commonly known as Teflon, is the most chemical resistant plastic out there. It has a unique non-stick surface that very few materials can adhere to. Those that can stick to Teflon, can be easily peeled of rubbed off. PTFE is flame resistant and FDA Compliant.
OVERVIEW
Teflon has excellent thermal and electrical insulation properties and a low coefficient of friction. PTFE’s mechanical properties are lower than other engineering plastics, but that can be improved by adding fillers such as glass fiber, carbon, or graphite. Royal Custom Plastics utilizes PTFE to machine precision parts for the food and industrial industry. Teflon is a great material to use for parts such as sleeves, plugs, bushings, gaskets, split rings, filter screens, slide guides, pivoting mounts, wear pads and idlers. Royal works with Glass, Carbon and Graphite Filled Teflon to make our customers machined parts perfect for the application they are using it for.
HEAT & CHEMICAL RESISTANCE
- Working Temperature Range of -400° F to 500° F
- Highest range of Chemical Resistance
MECHANICAL PROPERTIES
- Machines Easily when Chilled
- Not Easily Glued or Welded
- Excellent choice for Gaskets, Rings, Bearings
- Resistant to Weathering
- High Impact Strength
UL94 FLAME CLASSIFICATION
Teflon is rated V-0, Vertical Burn. Burning stops within 10 seconds, no flaming drips are allowed.
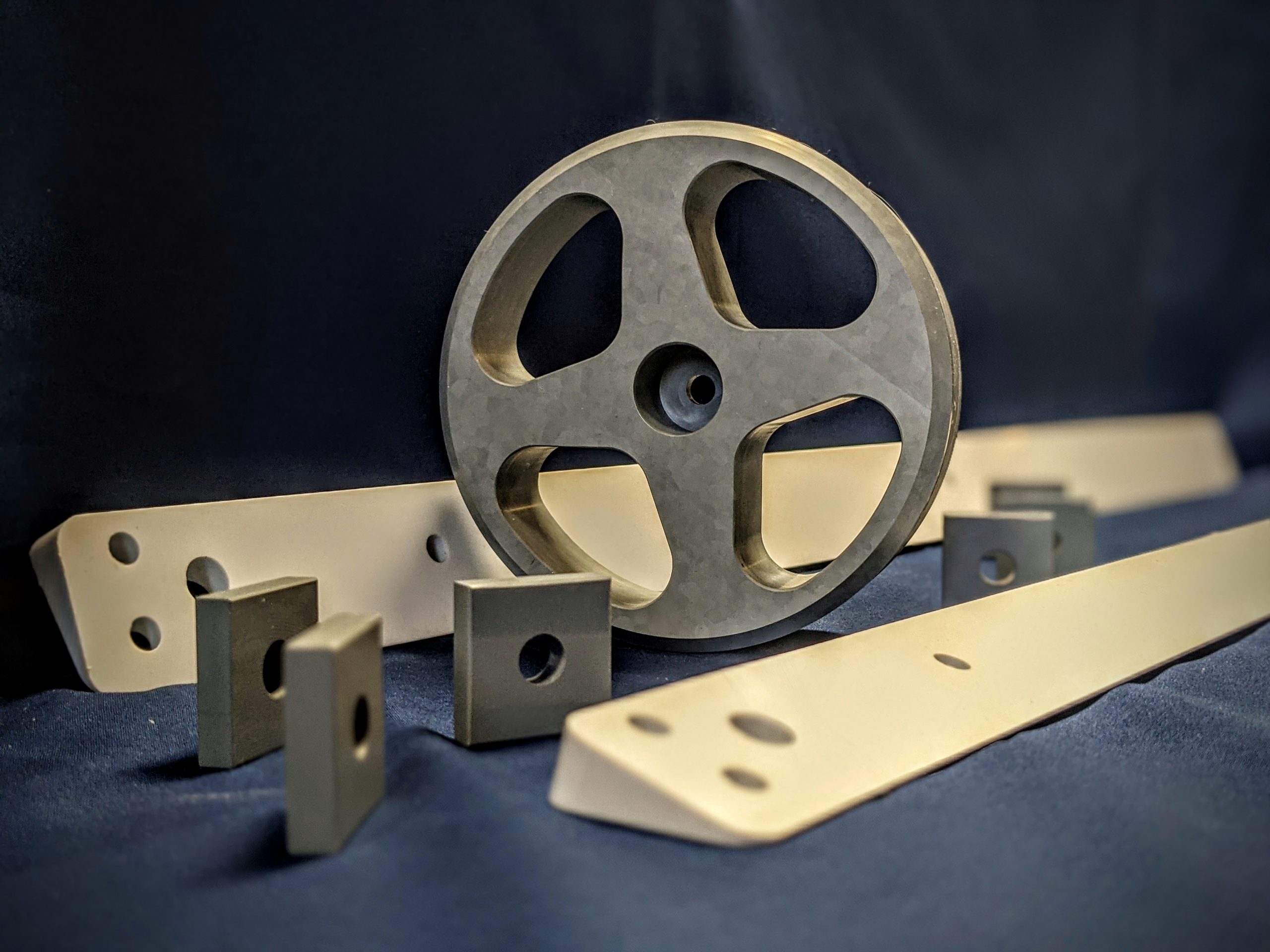
PVC / CPVC
PVC is a major player in the most used member of the Vinyl family. By adding the Chlorine atom, the outcome is CPVC. Both PVC and CPVC are generally low cost and most often used when corrosion resistance is necessary.
OVERVIEW
CPVC is PVC, but with a higher heat resistance and an improved fire and chemical resistance. PVC’s ideal characteristics consist of exceptional strength to weight ratio, ease of fabrication, cost efficiency, weather resistance, good impact resistance, and electrical and thermal insulator. Any applications that require extreme durability make PVC and CPVC a great choice.
Royal Custom Plastics has machined and fabricated with both materials. We utilize PVC and CPVC for applications such as hoods, ducts, process tanks, self-supporting tanks and tank linings, spacers and flanges and so much more!
HEAT & CHEMICAL RESISTANCE
- Exceptional Resistance to Chemicals and Corrosion
- CPVC Maximum Service Temperature is up to 200° F
- PVC Maximum Service Temperature is up to 140° F
MECHANICAL PROPERTIES
- Excellent Stiffness
- Good Impact resistance
- Ease of Machinability
- Weldable
UL94 FLAME CLASSIFICATION
PVC is rated V-O, Vertical Burn. Burning stops within 10 seconds, no flaming drips are allowed.
CPVC is rated V-0 Vertical Burn. Burning stops within 10 seconds, no flaming drips are allowed, 5VB -Surface burn, burning stops within 60 seconds, test specimens MAY HAVE burn-through. 5VA – This rating is the most flame retardant. Surface burn, burning stops within 60 seconds, test specimens MAY NOT have burn through.
STYRENE
Polystyrene, commonly known as Styrene, is a material that is die cuttable, screen printable, and has great thermoformability. The FDA has approved this material to be safe to use for food applications.
OVERVIEW
Styrene has a high degree of hardness and low moisture absorption. It is widely used for graphic art applications because of its excellent ink adhesion properties, color qualities, and low cost. Styrene holds its dimensions well under normal use. However, it should not be used outdoors on a continual basis. Most foods, drinks and common household acids have no effect on Polystyrene. On the other hand, cleaning solutions, citrus fruit, nail polish / remover, gasoline and turpentine will attack it.
Royal Custom Plastics supplies the food and dairy industry with thermoformed food pans and trays. We also utilize Styrene for name plates and POP signs.
HEAT & CHEMICAL RESISTANCE
- Becomes Malleable at 212° F
- Chemically Inert
- Resistant to Acids and Bases
- Easily Dissolved by Chlorinated Solvents
- Easily Dissolved by Aromatic Hydrocarbon Solvents
MECHANICAL PROPERTIES
- Easily Fabricated
- Medium to High Tensile Strength
- Poor Impact Strength
UL94 FLAME CLASSIFICATION
Polystyrene is rated HB, horizontal burn; slow horizontal burn test is considered “self-extinguishing”. This is the lowest (least flame retardant) UL94 rating.
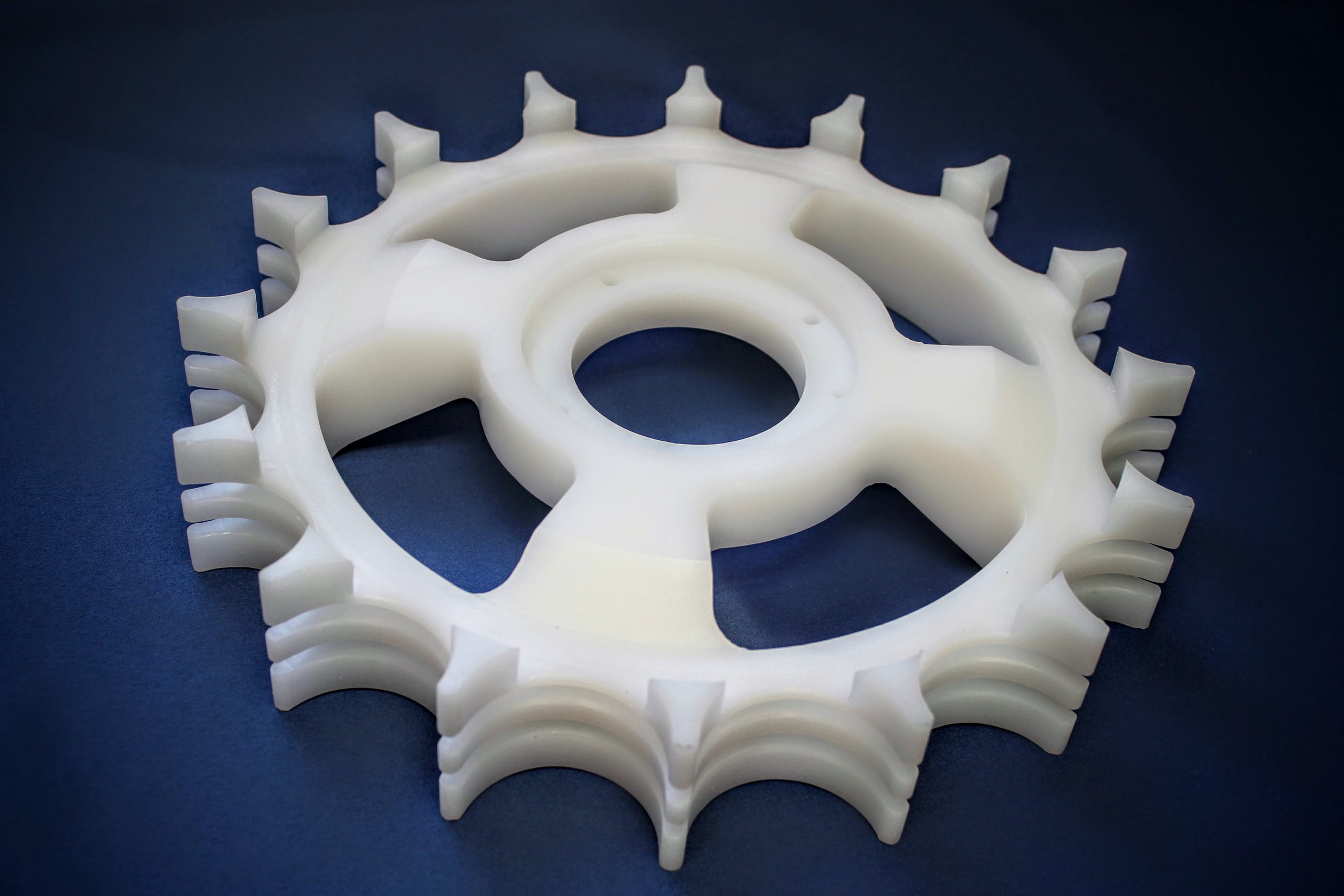
UHMW
Ultra-High-Molecular-Weight Polyethylene (UHMW) is a part of the Thermoplastic Polyethylene Family. UHWM is known for having the highest impact strength of all the presently made thermoplastics. It embodies all the characteristics of HDPE with the added trait of being resistant to concentrated acids and alkalis as well as numerous organic solvents. UHMW is FDA and USDA approved.
OVERVIEW
UHMW is great for both the paper industry and the food industry. In the paper industry, pulping and finishing operations require good wear resistance and low friction properties in both wet and dry applications. In the food industry, UHMW is the ideal material because of its resistance to abrasion and chemical attacks. The industrial grade UHMW is also perfect for both applications because it combats against stains and odors.
UHMW comes in many different colors and it also has many variants such as Metal Detectable, Ultraviolet Resistant, and Static Dissipating.
Here at Royal Custom Plastics, we do precise machining with UHMW. Royal utilizes UHMW for many machined products such as, Bearings, Bearing Shields, Seals, Chutes, Guide Plates, Rollers, Rails, Paddles Star Wheels, Gears and Cam Rollers to name a few!
HEAT & CHEMICAL RESISTANCE
- Melting Point of 267° F
- Excellent Chemical Resistance
MECHANICAL PROPERTIES
- Abrasion Resistant
- Corrosion Resistant
- Self-Lubricating
- No Moisture Absorption
- High Impact Strength
- Buoyant
- Extremely Low Coefficient of Friction
UL94 FLAME CLASSIFICATION
UHMW is rated HB, horizontal burn; slow horizontal burn test is considered “self-extinguishing”. This is the lowest (least flame retardant) UL94 rating.
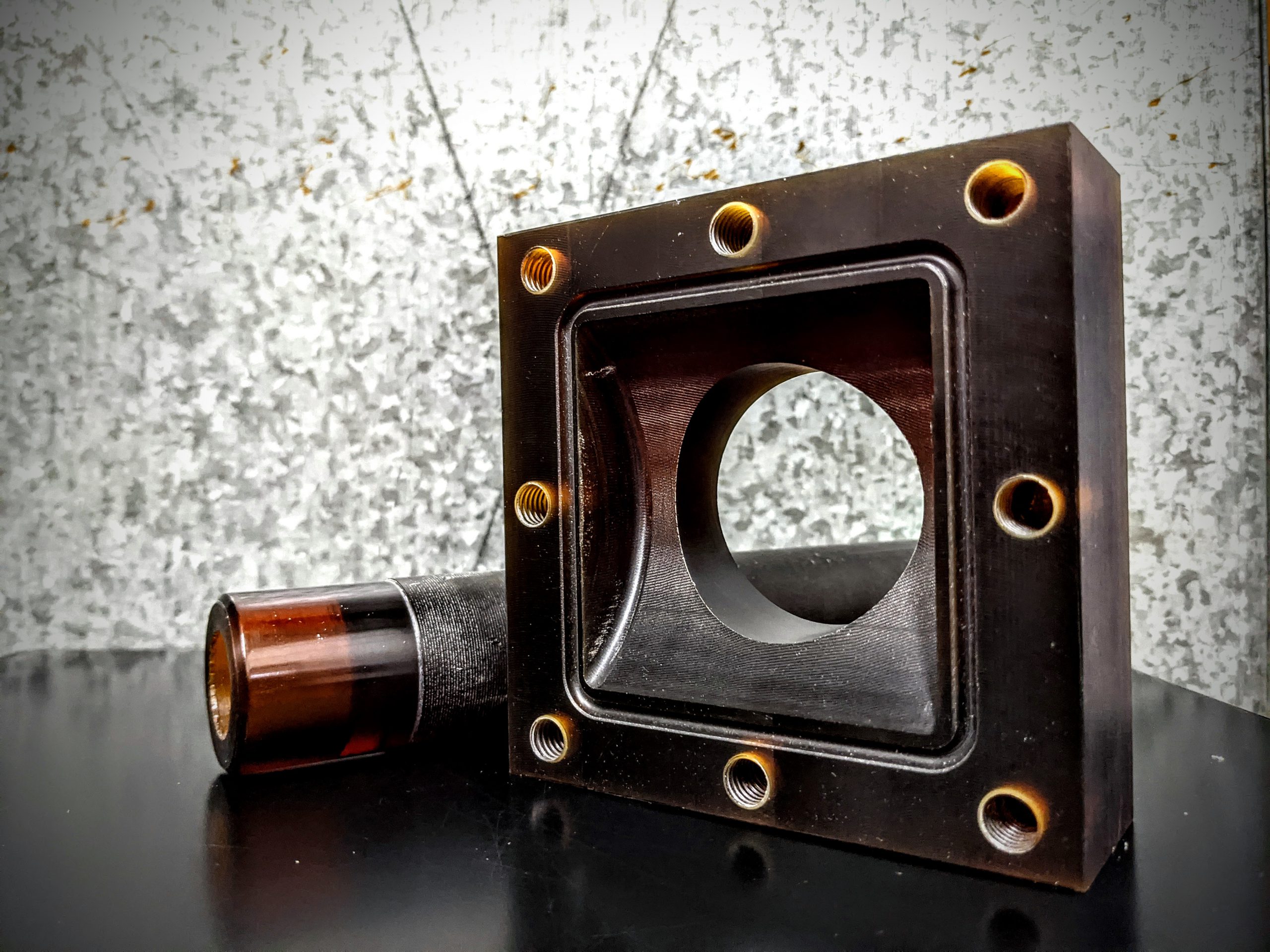
ULTEM
Polyetherimide (PEI), more commonly known as its trade name Ultem, is an amber-to-transparent thermoplastic. It has similar characteristics as PEEK but comparatively lacks when it comes to impact strength and usable temperature.
OVERVIEW
Ultem, is an exceptional material offering above average performances in mechanical, thermal, and electrical properties. It is a material that is FDA approved which makes it a strong candidate for medical applications. Ultem is also widely used in the electrical market because of its good arc resistance and dielectric constant. PEI offers high strength and excellent resistance to flame and heat.
HEAT & CHEMICAL RESISTANCE
- Heat and Solvent Resistant
- Flame Resistant
- Extremely low smoke generation
- Prone to Stress Cracking in Chlorinated Solvens
- Performs in Continuous use to 350° F
- Glass Transition Temperature is 420° F
MECHANICAL PROPERTIES
- High Dielectric Strength
- Arc Resistance
- Stress Resistant
- Rigid and Strong
- Resistant to Environmental Forces
UL94 FLAME CLASSIFICATION
Teflon is rated V-0, Vertical Burn. Burning stops within 10 seconds, no flaming drips are allowed.
VIVAK / PETG
PETG is the trade name for Vivak. This plastic is a clear transparent Co-Polyester that offers a unique balance of physical properties and ease of fabrication. PETG has a superior impact strength when compared to Acrylic and is more cost effective than Polycarbonate. However, it is easily scratched. Vivak is produced using resin that complies with FDA regulations for food contact applications.
OVERVIEW
PETG is widely used for food and beverage containers. It is also a prime candidate for thermoforming and vacuum forming. PETG is naturally colorless but like Acrylic, can come in a wide variety of colors. Royal Custom Plastics utilizes PETG for fabrication of parts such as deli trays, custom funnels and most recently, incubator boxes.
HEAT & CHEMICAL RESISTANCE
- Can withstand a continuous Temperature of 145° F
- Good Barrier to Alcohol
- Good Chemical Resistance
- May lead to longer fixturing time.
MECHANICAL PROPERTIES
- FDA Compliant
- Good Impact Strength
- Ideal for Thermoforming
- Lightweight
UL94 FLAME CLASSIFICATION
Vivak is rated V-2, Vertical Burn. Burning stops within 60 seconds, flaming drips are allowed. And HB, Horizontal Burn. Slow Horizontal Burn test are considered “Self-Extinguishing”. This is the lowest (least flame retardant) UL94 Rating.
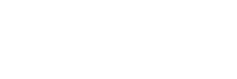
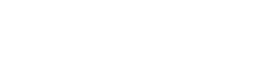
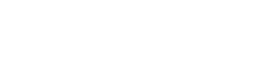

OUR PRODUCTS IN ACTION
MORE

ABOUT OUR PLASTICS
MORE

GET A QUOTE
MORE

NAVIGATION
PLASTICS
CONTACT
Royal Custom Plastics
1709 Suburban Drive
De Pere, WI 54115
Phone: 800-371-4383
(920) 983-1315
Copyright © 2025 Royal Custom Plastics